Posts: 214
Threads: 19
Joined: Oct 2014
Location: SOUTH AFRICA,KZN,DURBAN
03-08-2015, 04:03 PM
(This post was last modified: 03-08-2015, 04:07 PM by aRM.)
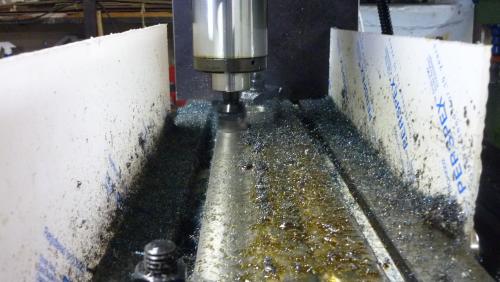
Hello there Folks
Seeing that somebody was averse to the "too clean" look of our Mill, we did have a project to complete and took pics using our new KYOCERA MTP 90 CERATIP Facemill with the CERMET TN-60 Carbide Inserts, supposedly a HIGH-FEED HIGH CUTTING Tool - which we had seen in action on a popular channel, and which really created enough swarf to not only mess up our Machine but the whole area around it.
Our patient wait of some 6 weeks for the Tool to arrive was, to say the least, a bit disappointing. We had an proper opportunity to give this tool a run on a 24" piece of D2 which required just 1.5mm take-down.
On the first run the Tool seemed to have lost it depth of cut nearing the end of the workpiece, although we had torqued the Draw Bar adequately. We initially commenced cutting longitudinally, on the Auto Feed, but encountered too loud complaining from the Tool. Switching over to cutting in the Y direction manually seemed more pleasing to the Tool !!! However, this left those numerous ugly division cut-lines which we eventually removed switching to the X Auto Feed. (Hope we have our X's and Y's correct !!!)
During the cut the Inserts eventually worked themselves loose with 2 falling out completely !!! This was frightening. We have an Mitsibushi Octoturn 50 mm Facemill, or something called that, which feeds much slower, but which never behaved that way.
We were really anticipating this MTP Tool to plough through the D2 and get finished in no time. We did use it initially on another large Knife for Son, also on D2, with no drama. But working on this large piece seemed to have drained the Tool totally !!! After the inserts loosened and fell off we started afresh with 2 new Inserts, the one was still good, torqued them solid from the rear and found our bearings, somewhat.
We have attached progressive pics for verification commencing with the Full Length view, some of the Y cut, then the X run and the final finish cuts with cutting fluid only. (This should please the avid eye ballers)
Finally, and this leads us to finding out from U Folks if there is a better Tool out there or by the limitations of our knowledge and experience, we had executed something/s totally wrong here. "The fault dear Brutus lies not in our stars, but in ourselves" !!!
Would be nice to hear from U Guys.
Thanks in advance
Regards
aRM
Posts: 8,746
Threads: 314
Joined: Feb 2012
Location: Arizona/Minnesota
Don't let Ken catch you using coolant or cutting oil with those inserts.
What size mill do you have? Can you post a picture of the mill?
Ed
Posts: 214
Threads: 19
Joined: Oct 2014
Location: SOUTH AFRICA,KZN,DURBAN
03-08-2015, 04:45 PM
(This post was last modified: 03-08-2015, 04:46 PM by aRM.)
Hello Ed
We have a full-sized Bridgeport clone.
BTW, who is KEN ???
Thought about not using coolant, but then again that's still to be hardened D2 and did not want to jeopardise the steel grain structure.
aRM
Posts: 2,685
Threads: 29
Joined: Feb 2012
Location: Nova Scotia, Canada
The following 2 users Like stevec's post:
EdK (03-08-2015), PixMan (03-08-2015)
03-08-2015, 05:20 PM
(This post was last modified: 03-08-2015, 05:21 PM by stevec.)
Ken is Pixman, man! The most knowledgeable insert man in the universe.
(how's that for a suck-up Ken?)
Steve
Busy Bee 12-36 lathe, Busy Bee Mill drill, Busy Bee 4x6 bandsaw, Homemade 9x17 bandsaw, Ad infinitum.
Posts: 2,344
Threads: 53
Joined: Feb 2012
Location: Spencer MA USA
The following 2 users Like PixMan's post:
Mayhem (03-09-2015), aRM (03-09-2015)
LOL...too funny.
I wouldn't buy one those cutters that use a TPG insert (actually sold one I had.) They absolutely hammer the spindles and you just found out what else happens to an insert that has a smooth top and very little holding it in.
On face milling I use a lead angle cutter, specifically a Walter F4080 with octagonal inserts or a Walter F4033 which both give EIGHT edges per insert rather than three. Cost per edge is far cheaper. They have a grade WKP25S that just kicks butt in tool steels. Here's what they look like:
The one on the left is an F4080, the next one over is my F4033, the black one is an F2280 (renamed F4080 with the nickel plating). The one on the right is an F4042 shoulder mill that I sold off to get an F4041 (4 edges per insert rather than 2), just like the ones EdK, Wrustle and "the penguin" (Jack) all have.
Being a machinist for a living, I have many friends who own shops. One is a place that makes broaches out of one of the toughest HSS tool steel I've ever seen, CPM T15. They were using a 2" 5-insert Seco cutter similar to that F4042 with two-edge inserts and getting 2 passes at 3mm deep x 1-3/4" wide x 28" long, per edge. Index the inserts, take one more pass, flip the part around, take another pass, change inserts, make the last pass, and so on. So it took (effectively) 7.5 inserts per part.
They bought the 2" 4-insert Walter F4041 and the LNGX130708R-L55 inserts in that grade WKP25S to try. At the same spindle speed and inches per minute feed they went 4.5mm deep, took two passes, flipped the part over, took two passes, part done. Two more complete parts and it looked to be time to index the inserts to the second edge (of four.) But they did one more part complete instead. So, 4 inserts did 16 parts. Seco inserts, 16 parts were using 120 inserts.
Think about that. The Walter inserts cost $22 each, the Seco were $17. Which ones are truly cheaper?
Check eBay for a cutter and end your troubles. New ones are pricey, but in a commercial shop that kind of payback makes the initial cost go bye-bye fast.
And for the record, they used flood coolant for the tool steel, and I would too. That stuff can act VERY weird if you get it too hot!
Posts: 2,685
Threads: 29
Joined: Feb 2012
Location: Nova Scotia, Canada
(03-08-2015, 06:26 PM)PixMan Wrote: So it took (effectively) 7.5 inserts per part.
Ken, did you mean 7.5 "passes" per part?
Or am I (as usual) "out to lunch"?
Steve
Busy Bee 12-36 lathe, Busy Bee Mill drill, Busy Bee 4x6 bandsaw, Homemade 9x17 bandsaw, Ad infinitum.
Posts: 2,344
Threads: 53
Joined: Feb 2012
Location: Spencer MA USA
(03-08-2015, 06:51 PM)stevec Wrote: (03-08-2015, 06:26 PM)PixMan Wrote: So it took (effectively) 7.5 inserts per part.
Ken, did you mean 7.5 "passes" per part?
Or am I (as usual) "out to lunch"?
Steve

No, Steve, I meant what I wrote. The cutter takes 5 inserts, each has two edges. By the time one part is done (six 3mm deep passes, 3 each side), both edges of one set of five inserts are toast, plus ONE edge of the second set of five.
Make sense?
Posts: 2,685
Threads: 29
Joined: Feb 2012
Location: Nova Scotia, Canada
Sorry!
Busy Bee 12-36 lathe, Busy Bee Mill drill, Busy Bee 4x6 bandsaw, Homemade 9x17 bandsaw, Ad infinitum.
Posts: 2,344
Threads: 53
Joined: Feb 2012
Location: Spencer MA USA
(03-08-2015, 07:11 PM)stevec Wrote: Sorry! 
Please Steve, no need to apologize! I just wasn't clear in how I wrote it. I'm the one who should be apologizing for not making sense.
It was pretty dramatic in how they saved so much time by going to two 4.5mm deep cuts per side instead of three 3mm cuts, but the tool life was most telling. Just the saved downtime from not changing inserts every hour was huge, though when you add in the tool savings it was over $120,000 a year for them.
Posts: 137
Threads: 16
Joined: Jan 2015
Location: Oxford, CT
I use a Valenite V555 2" face mill that uses 4 pentagon cutters. I'm very happy with it and it leaves a beautiful finish!
|