Posts: 3,795
Threads: 183
Joined: Jun 2012
Location: Farmington Hills, Michigan
The following 1 user Likes TomG's post:
Wongster (12-16-2018)
Tungsten is hard and not very ductile so it can be a challenge to machine. It requires sharp carbide tooling with lots of clearance and relief, That fact and the high temperatures generated causes the tooling to wear very quickly, so keep and eye on it. Cutting speeds are similar to grey iron but with slower feed rates. If you try to push it, it pushes back big time. Rigid setups are also necessary due to the high machining forces and any chatter will chip the tool.
It's been a while since I've machined tungsten, but I definitely don't miss it.
Tom
Posts: 642
Threads: 14
Joined: Oct 2013
Location: East Sussex, UK
The following 1 user Likes awemawson's post:
Wongster (12-16-2018)
I'd do it with a sinker EDM, simple domed copper electrode and off you go. EDM doesn't much care how hard materials are !
Andrew Mawson, proud to be a member of MetalworkingFun Forum since Oct 2013.
Posts: 239
Threads: 2
Joined: Sep 2016
Location: California & Wales Home & Home Away
The following 1 user Likes Mike E.'s post:
Wongster (12-16-2018)
You might want to consider "slightly" shortening the tungsten barrels in the lathe, which should allow you to more easily remove minute amounts of material and accurately establish equal weight for the set. Also, using wire flight shafts which come in different lengths can reduce weight.
Posts: 301
Threads: 30
Joined: Mar 2012
Location: Singapore
(12-15-2018, 11:07 AM)TomG Wrote: Tungsten is hard and not very ductile so it can be a challenge to machine. It requires sharp carbide tooling with lots of clearance and relief, That fact and the high temperatures generated causes the tooling to wear very quickly, so keep and eye on it. Cutting speeds are similar to grey iron but with slower feed rates. If you try to push it, it pushes back big time. Rigid setups are also necessary due to the high machining forces and any chatter will chip the tool.
It's been a while since I've machined tungsten, but I definitely don't miss it.
Tom
Thank you, Tom. I've not done grey iron before. Given that I'll be using a 3mm drill, what's the recommended speed?
I'll visit the hardware shop near my office tomorrow to see if I can pick up a couple of carbide drill.
Regards,
Wongster
Posts: 301
Threads: 30
Joined: Mar 2012
Location: Singapore
(12-16-2018, 06:07 AM)Mike E. Wrote: You might want to consider "slightly" shortening the tungsten barrels in the lathe, which should allow you to more easily remove minute amounts of material and accurately establish equal weight for the set. Also, using wire flight shafts which come in different lengths can reduce weight.
I don't know anything about darts or the game. I was asked to take off about 2mm depth with a 3mm drill and see how much weight that will take off. I'll be advised from there if I need to drill a little off from the front hole.
Regards,
Wongster
Posts: 239
Threads: 2
Joined: Sep 2016
Location: California & Wales Home & Home Away
The following 1 user Likes Mike E.'s post:
Wongster (12-23-2018)
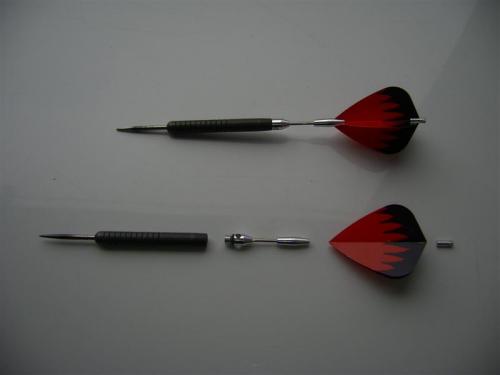
Here is an example of the short wire flight shafts which can reduce weight.
Posts: 3,795
Threads: 183
Joined: Jun 2012
Location: Farmington Hills, Michigan
The following 1 user Likes TomG's post:
Wongster (12-23-2018)
(12-16-2018, 08:46 AM)Wongster Wrote: Thank you, Tom. I've not done grey iron before. Given that I'll be using a 3mm drill, what's the recommended speed?
I'll visit the hardware shop near my office tomorrow to see if I can pick up a couple of carbide drill.
Regards,
Wongster
Even at a conservative 200 sfpm, a drill that small in carbide could be run at 6000-7000 rpm. Slower is ok for drilling because it doesn't increase the side load as with an end mill.
Tom
Posts: 301
Threads: 30
Joined: Mar 2012
Location: Singapore
The following 1 user Likes Wongster's post:
Mike E. (12-24-2018)
I bought myself a couple of 3mm cobalt drills (the only type available other than HSS in the shop near my office). It managed to drill through the skin and from the feel I get when drilling further, the inside is softer than the skin.
Thanks for all your help in answering my questions.
Regards,
Wongster
Posts: 15
Threads: 6
Joined: Dec 2018
Location: USA
If you don't wanna buy carbide bits to try. I believe you can buy a masonry drill bit and sharpen it .most have a small carbide bit in the tip. I have never done this myself but have seen others do it successfully there's some threads on it if you Google it and some YouTube videos