I decided to work on some shop organization today, so I thought " why grovel through a box of 5C collets every time I want to grind a
tool or sharpen an end mill?" I got out he full set of collets I have and layed out a pattern of 2 rows.
I worked out some dimensions and rough cut a piece of ½" lexan (in inventory)'
I cleaned up the sides in the mill then set up to step out 2 rows of 8 1¼" holes for the collets.
Then I started figuring the best way to cut the holes.
I started with a 1" hole saw followed by a 1¼" 2 insert carbide end mill that I had.
It was a tight 1¼" so I adopted a teeny fly cutter with a tool set to a "large" 1¼".
The hole saw hole was fine except for the fact that even with coolant and frequent chip clearing there was still a "slug" that had to
be "punched" out from both side slots.
So I switched to a the shortest "large" drill I had
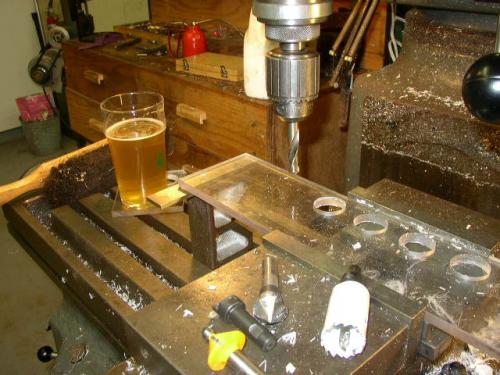
(I'm trying to keep the procedure from one hole to the next as smooth as
possible.) Ooops ther's a shot of my homemade European lager.
and followed with a countersink
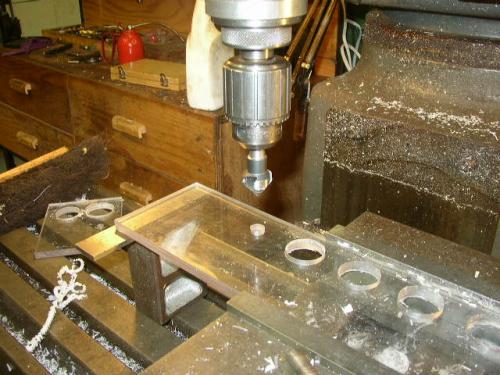
and then a router bit
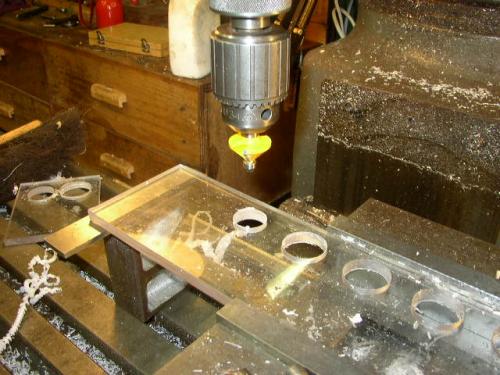
that brought me back to the point where my little flycutter/
boring tool gave me the finish and size I wanted.
We're down to 4 tools but at least no height changes.
A little bravado and I decided I could eliminate the "wrongly used" router bit with a little grind on the fly cutter tool.
Success, we're down to 3 tool changes no spindle speed changes and no up and down for the knee.
Here's the rack on the wall behind the T&C grinder.
Busy Bee 12-36 lathe, Busy Bee Mill drill, Busy Bee 4x6 bandsaw, Homemade 9x17 bandsaw, Ad infinitum.